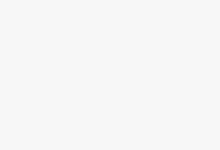
Microchip Corporation Utilizes Digital Feedback Loops to Customize Power Products Freely
Solving increasingly pressing power regulation and safety issues requires efficient and intelligent power supplies that provide external monitoring capabilities and can be cost-effectively manufactured with minimal hardware changes.
Advances in power technology have shown that digital control of power conversion feedback loops can help designers create accurate and reliable power supplies with higher power densities, at a lower cost and faster to market. These digital power supplies can be easily customized at any point in the production process, as full modifications can be implemented in software rather than hardware.
Analog feedback circuits are still of great interest in DC-to-DC power supplies less than 100W and AC-to-DC power supplies less than 250W. In high-performance, high-grade power supplies, however, digital control of the power-conversion feedback loop is increasingly important because it overcomes most of the limitations sometimes imposed by fixed analog technology.
For example, capacitive loads can significantly affect the stability of the power supply. While analog feedback systems can also handle capacitive loads, large changes in load capacitance can exceed the phase and gain margins of the design. The advantage of a digital feedback system is that it can change the compensation method at any time, allowing the feedback loop to compensate for a wider range of changes in load characteristics in real time.
Move to digital
Until recently, digital feedback systems were rarely used because of their complexity, the high cost of the required DSP, and the limited functionality of the DSP peripherals. With training, however, the perceived complexity is being reduced, and the introduction of digital signal controllers (DSCs) is helping to alleviate issues related to cost and peripheral functionality.
DSC fully combines the look and feel of an MCU with the computing and processing power of a DSP. The CPU design employs the mathematical functions typically found in DSPs, while the functionality and flexibility of peripherals can be traced back to embedded controllers. Therefore, the current DSC has the mathematical performance of DSP, but also maintains the flexibility and complex peer-to-peer characteristics of peripherals. DSC greatly reduces design complexity and achieves design goals without consuming CPU performance.
In fact, with the support of these capabilities, designs using DSCs are indeed much simpler than DSP designs, since many DSCs integrate power-specific on-chip peripherals. This peripheral includes a counter-based pulse width modulation (PWM) module, an analog comparator, and an analog-to-digital converter (ADC), thus enabling an analog comparator-based feedback loop and ADC sampling. These capabilities, coupled with fast multiplication in a single clock cycle, allow the DSC to easily provide the high execution rates required by power control loop software.
The capabilities of the DSC and the lower switching frequency of the high-power design allow a DSC with the right peripherals but modest performance to easily handle multiple control loops. This means that a single chip can not only improve the response characteristics of the power supply, but also do it for multiple independent outputs simultaneously.
Before starting a power supply design, designers must make three basic choices:
1. What topology is used in the design?
2. What working mode is used?
3. What control methods are used?
The topology depends primarily on the input-to-output voltage ratio of the design. The mode of operation depends on the topology and required output current as well as the cost associated with the components. Finally, the control method usually depends on the technology available and the cost of the device to a lesser extent. Each of these options is discussed in detail below, and it is indicated how the use of DSC will affect these options.
topology
As mentioned above, the topology mainly depends on the output-to-voltage ratio of the design. Designs with higher input voltages typically use a buck topology, while designs with lower input voltages typically use a boost topology. However, another factor that affects topology selection is a PWM controller with the necessary features that are compatible with the chosen topology. After all, a switch-mode power supply (SMPS) is impossible if the designer cannot generate the correct switching signals.
This is where DSC comes in. Since the DSC’s peripherals are programmable, single-phase PWM outputs, two- or three-phase PWM outputs, half-bridge drive outputs and even full H-bridge drive outputs can be generated. In fact, due to the programmability of the DSC peripheral, a given topology need not remain the same.
To prevent shoot-through currents, the DSC may employ dead-time control circuits between the bridge outputs.
Switching from single-phase to two-phase and then three-phase while maintaining a reasonable phase shift between phases is well within the capabilities of the DSC. Some DSCs even include dead-time control between bridge outputs, which can be used to prevent shoot-through currents in synchronous switching designs.
Operating mode
The next issue to consider is the working mode. Typically analog designs operate in either continuous Inductor current or discontinuous inductor current mode. These two modes have their own unique advantages. The discontinuous power mode design maintains a regulated voltage even when the output current is as small as zero. The continuous design uses smaller magnetic components and has tighter control over the output voltage ripple. Until recently, the industry has not been able to effectively integrate the two modes because they have different feedback requirements.
However, the DSC’s programmable peripherals can be reconfigured at any time while the design is working. This means that DSC-based designs can switch between different operating modes, switching to continuous mode for stable operation when the output current is high enough, and then switching to discontinuous mode when the output current drops low enough.
While an analog design can certainly perform the same transitions, it requires two feedback paths (one for each mode) with transient glitches on transitions. So DSC has the added advantage that only one feedback path is required. Because it is a software-based feedback technique, the storage elements of the feedback filter can be preloaded to avoid transition glitches (Figure 2).
The DSC has the flexibility to change the mode of operation.
Solving increasingly pressing power regulation and safety issues requires efficient and intelligent power supplies that provide external monitoring capabilities and can be cost-effectively manufactured with minimal hardware changes.
Advances in power technology have shown that digital control of power conversion feedback loops can help designers create accurate and reliable power supplies with higher power densities, at a lower cost and faster to market. These digital power supplies can be easily customized at any point in the production process, as full modifications can be implemented in software rather than hardware.
Analog feedback circuits are still of great interest in DC-to-DC power supplies less than 100W and AC-to-DC power supplies less than 250W. In high-performance, high-grade power supplies, however, digital control of the power-conversion feedback loop is increasingly important because it overcomes most of the limitations sometimes imposed by fixed analog technology.
For example, capacitive loads can significantly affect the stability of the power supply. While analog feedback systems can also handle capacitive loads, large changes in load capacitance can exceed the phase and gain margins of the design. The advantage of a digital feedback system is that it can change the compensation method at any time, allowing the feedback loop to compensate for a wider range of changes in load characteristics in real time.
Move to digital
Until recently, digital feedback systems were rarely used because of their complexity, the high cost of the required DSP, and the limited functionality of the DSP peripherals. With training, however, the perceived complexity is being reduced, and the introduction of digital signal controllers (DSCs) is helping to alleviate issues related to cost and peripheral functionality.
DSC fully combines the look and feel of an MCU with the computing and processing power of a DSP. The CPU design employs the mathematical functions typically found in DSPs, while the functionality and flexibility of peripherals can be traced back to embedded controllers. Therefore, the current DSC has the mathematical performance of DSP, but also maintains the flexibility and complex peer-to-peer characteristics of peripherals. DSC greatly reduces design complexity and achieves design goals without consuming CPU performance.
In fact, with the support of these capabilities, designs using DSCs are indeed much simpler than DSP designs, since many DSCs integrate power-specific on-chip peripherals. This peripheral includes a counter-based pulse width modulation (PWM) module, an analog comparator, and an analog-to-digital converter (ADC), thus enabling an analog comparator-based feedback loop and ADC sampling. These capabilities, coupled with fast multiplication in a single clock cycle, allow the DSC to easily provide the high execution rates required by power control loop software.
The capabilities of the DSC and the lower switching frequency of the high-power design allow a DSC with the right peripherals but modest performance to easily handle multiple control loops. This means that a single chip can not only improve the response characteristics of the power supply, but also do it for multiple independent outputs simultaneously.
Before starting a power supply design, designers must make three basic choices:
1. What topology is used in the design?
2. What working mode is used?
3. What control methods are used?
The topology depends primarily on the input-to-output voltage ratio of the design. The mode of operation depends on the topology and required output current as well as the cost associated with the components. Finally, the control method usually depends on the technology available and the cost of the device to a lesser extent. Each of these options is discussed in detail below, and it is indicated how the use of DSC will affect these options.
topology
As mentioned above, the topology mainly depends on the output-to-voltage ratio of the design. Designs with higher input voltages typically use a buck topology, while designs with lower input voltages typically use a boost topology. However, another factor that affects topology selection is a PWM controller with the necessary features that are compatible with the chosen topology. After all, a switch-mode power supply (SMPS) is impossible if the designer cannot generate the correct switching signals.
This is where DSC comes in. Since the DSC’s peripherals are programmable, single-phase PWM outputs, two- or three-phase PWM outputs, half-bridge drive outputs and even full H-bridge drive outputs can be generated. In fact, due to the programmability of the DSC peripheral, a given topology need not remain the same.
To prevent shoot-through currents, the DSC may employ dead-time control circuits between the bridge outputs.
Switching from single-phase to two-phase and then three-phase while maintaining a reasonable phase shift between phases is well within the capabilities of the DSC. Some DSCs even include dead-time control between bridge outputs, which can be used to prevent shoot-through currents in synchronous switching designs.
Operating mode
The next issue to consider is the working mode. Typically analog designs operate in either continuous inductor current or discontinuous inductor current mode. These two modes have their own unique advantages. The discontinuous power mode design maintains a regulated voltage even when the output current is as small as zero. The continuous design uses smaller magnetic components and has tighter control over the output voltage ripple. Until recently, the industry has not been able to effectively integrate the two modes because they have different feedback requirements.
However, the DSC’s programmable peripherals can be reconfigured at any time while the design is working. This means that DSC-based designs can switch between different operating modes, switching to continuous mode for stable operation when the output current is high enough, and then switching to discontinuous mode when the output current drops low enough.
While an analog design can certainly perform the same transitions, it requires two feedback paths (one for each mode) with transient glitches on transitions. So DSC has the added advantage that only one feedback path is required. Because it is a software-based feedback technique, the storage elements of the feedback filter can be preloaded to avoid transition glitches (Figure 2).
The DSC has the flexibility to change the mode of operation.
Control Method
The final design choice is in the control method of the design, whether to use voltage-mode or current-mode control. Traditional analog SMPS designs use one of these two control techniques, ultimately depending on cost and available technology.
Voltage-mode control is an older method that was often used in most early SMPS designs. It converts the error signal from the error amplifier/loop filter to PWM pulse width using a ramp generator and voltage comparator. Simple voltage-mode control methods have three fundamental limitations. First, there is no current limiting mechanism to protect the circuit components. Second, it responds slowly to input or output transients. Third, it creates an unstable feedback loop.
Current mode control is a better and safer control method and it consists of a double loop format. The inner current loop is designed to charge the inductor to the peak current specified by the output voltage loop. The outer loop is similar to the feedback loop of voltage mode control and is primarily used to monitor the output, phase/frequency compensate the feedback, and regulate the energy delivered by the current loop.
Because the inner loop adjusts the inductor current on a cycle-by-cycle basis, the inductor doesn’t actually remember the last pulse and doesn’t carry the energy from the previous cycle. It also provides peak current protection for transistors, eliminates “ratcheting” in magnetics, suppresses changes in input voltage, and provides convenient control loop compensation.
Efficient implementation of current-mode control in digital SMPS designs relies on the use of DSCs. The DSC has an on-board PWM peripheral that operates in the same way as a current-mode PWM generator (Figure 3). The difference is the output of the digital feedback. Voltage-mode designs use feedback to directly control the duty cycle of the PWM. In a current-mode design, the DSC’s PWM has a comparator-based pulse termination feature that adjusts the pulse width based on current feedback, and the digital-to-analog converter (DAC) output is driven by digital feedback.
Current-mode control is achieved by calculating the PWM frequency and maximum duty cycle required by the SMPS design, and then configuring the PWM counter with these parameters. This sets the maximum duty cycle and pulse frequency of the system. The design must then adjust the reference DAC output to handle the expected maximum range of current feedback signals. Doing so provides the highest resolution when controlling the PWM duty cycle.
Finally, the special proportional-integral-derivative (PID) software routines needed to control and stabilize the system must also be developed. This routine must provide an appropriate feedback signal based on the feedback voltage from the ADC to achieve stable performance. In addition, the routine must compare this feedback signal with its own internal digital parameters and output the ideal current setting to the DAC that generates the comparator reference signal (Figure 3).
This SMPS design uses DSC-based digital current-mode control.
digital loop control
A key factor to consider when using a DSC for an SMPS design is to ensure that the on-board PWM module provides sufficient resolution for the power supply design. The ADC of the DSC is to provide state (feedback) to the control loop and therefore should also have sufficient resolution.
Second, it is also important to choose the DSC carefully. The analog comparator built into the DSC must be fast enough to match the pulse width generated. While ADCs can be used in place of comparators to terminate PWM pulses, the DSC must continuously monitor and process the signal. This would waste their processing power, since the monitored signal is only compared to fixed limits. High-speed analog comparators free the processor and ADC to perform other higher-value tasks, while helping the DSC perform power-fail and current-limiting functions.
Additionally, it is useful for the ADC module in the DSC to provide independent sample-and-hold circuits that allow the DSC to simultaneously sample multiple voltages or currents at precise times. This allows even transient signals to be sampled and helps reduce system cost. It would be better if the ADC could sample asynchronously, as this would support multiple control loops operating at different frequencies, such as a power factor correction (PFC) circuit running at 70kHz and a DC-DC converter module running at 250kHz.
PID Algorithms in SMPS Design
Using the PID algorithm, the proportional, integral and differential errors between the actual voltage and the ideal output voltage are simultaneously used to control the PWM duty cycle. There are three basic forms of PID algorithm:
1. Serial, or interactive;
2. Parallel, or non-interactive;
3. Ideal parallelism.
PID algorithms can be deployed in both voltage and current mode control loops. In addition, DSCs do not require complex DSP programming skills because they provide DSP functionality as peripherals in the familiar MCU environment.
Duty cycles over 50% may create current-mode stability issues. However, this problem can be easily solved by setting the required current level through the PID software. This makes it easy to adjust the DAC value and makes it much easier to implement slope compensation digitally than analog, which requires a ramp generator synchronized with the PWM pulses and a summing point that adds the ramp to the current feedback.
The above techniques will generate current-mode SMPS designs based on economical and lower MIPS DSCs, rather than designs based on fast controllers running at 1 to 2 BIPS. For example, the dsPIC30F202X DSC from Microchip includes a high-resolution digital PWM generator, a nominal 2 million samples per second ADC, a high-speed analog comparator connected to a 10-bit reference ADC, and a 30-MIPS, DSP-enabled control device (Figure 4).
Lower MIPS economical DSCs like Microchip’s dsPIC30F202X do not use fast controllers running at 1 to 2 BIPS, but they provide the basis for current-mode SMPS designs.
The core of the control software is the PID control loop (Figure 5), which operates on an ADC interrupt on a fixed-time basis. Where should system functions like voltage rise/fall, error detection, forward feedback calculations, and communication support routines be located? Idle loop? in order to reduce unnecessary workload in the PID control software.
At the heart of the software is the PID control loop structure.
The PID loop is the most time-sensitive part of the software. So to ensure efficient use of DSC resources, the loop should not use more than 66% of the available processor bandwidth. This allows the design to have sufficient capacity to handle idle loop functions such as communications, or to support functions such as soft-start and sequencing.
In a SMPS application based on a 30MIPS DSC, this translates to a PID loop containing 30 instructions with an execution time of about 1µs. At a repetition rate of 500kHz (or 2μs), the PID control loop uses half the available processor bandwidth, or 15MIPS.
free innovation
There are many advantages to using digital feedback control for power supplies. The biggest advantage is that they have a lot of flexibility, giving designers the freedom to innovate their designs. As mentioned above, the designer’s primary concern is the availability of the technology needed to implement the design. The beauty of DSC is its configurability, which allows designers to create the right technology specifically for the target design.
For example, a power supply may need to coordinate multiple output voltages during startup and shutdown, or perform load or current sharing among a group of independent power conversion modules. In these cases, digital feedback control provides such functionality at no additional cost. Customizing power supplies using analog devices in these ways is quite expensive. Another advantage is the ability to make changes to the system at any time, or hot swapping capability. For example, if a power module fails in a telecom or other mission-critical application, service technicians can replace the defective power module with a new one while the system continues to operate. This hot-swap function would be very expensive to implement using analog components, but would be extremely cost-effective if it were a power supply digitally controlled by a DSC.
In addition, the DSC can also be easily reprogrammed if the power supply must be able to adapt to changing requirements. If it is an analog power supply design, you must start over with a new module. And thanks to the use of on-chip flash memory, DSC can simplify the power supply production assembly line. This means that a single hardware design can be configured to meet the voltage and/or current requirements of different users.
In addition, fine-tuning and calibration of the power supply can be achieved by programming the flash memory in the DSC. This method does not require trimmer tubes or laser trimmer resistors. Digital power supplies can also load test-friendly software for board testing, or generate multiple custom products from the same DSC hardware platform.
Summary of this article
In conclusion, the benefits of digital power conversion are numerous, and designers can obtain a convenient and cost-effective design by using a DSC with power-friendly on-chip peripherals. Digital power supplies give designers the freedom to innovate and develop power supplies with higher reliability, flexibility, and transient response, and can be easily customized later in production by modifying firmware rather than hardware.
The Links: NL6448AC33 K209A05