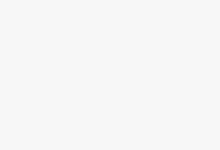
Researchers develop a new type of real-life combination that can test electric vehicle batteries under real conditions
China and Africa News, June 8, learned that researchers from the Fraunhofer Association in Germany have developed a new type of test environment that combines physical components with mathematical simulations of vehicles to test electric vehicle batteries under real conditions.
Electric vehicle batteries are usually called power batteries and are key components of electric vehicles. Storing the energy provided by the charging station and providing electricity on demand is one of the functions of the battery performance equation. The other is when dealing with sharp turns, bouncing on gravel roads full of potholes, and driving cars in the heat, the battery needs to resist the abrasion caused by electricity, mechanical and thermal stress. Therefore, the new battery system must undergo various tests before it can be installed on the vehicle.
However, traditional laboratory tests are far from reality. Real-world tests must wait until engineers have produced a prototype car that can be driven. If in the later stage, the battery has a problem that has not been discovered before, it may take a lot of time and money to improve the battery.
Researchers at the Fraunhofer Institute for Structural Durability and System Reliability LBF (Fraunhofer Institute for Structural Durability and System Reliability LBF) have developed an alternative MEF-BILL, which is Battery in the Loop. abbreviation of. LBF researchers said: “We are now introducing real road conditions into the laboratory, combined with multi-physical testing equipment and computerized vehicle simulation technology, which means that we can test the battery under real conditions before the prototype vehicle exists. In this way, we can invest a lot of time in the research and development process and can significantly improve the quality of battery research results.”
The load that the battery bears mainly comes from three aspects-the load mainly caused by current, vehicle movement and climatic factors. Traditional methods will test the above three factors separately in a laboratory with a standard operating environment. However, in the real world, the three factors are interdependent and affect each other in complex ways. Researchers can simultaneously test such loads and their interactions in the test environment, and integrate computerized vehicle models in the test environment in real time. In this way, researchers can simulate vehicles and their performance on different types of roads, so as to be able to determine the load that is common in the real world and will affect the battery under actual conditions.
In the past, laboratory tests on battery current distribution were usually carried out according to the ideal curve, but in real life the curve looks very different. The change trajectory is highly dynamic, changes randomly, and changes unpredictably and sharply with the appearance of load peaks. Therefore, researchers first need to determine the test conditions. What kind of car does this battery power? How heavy is the load? What’s the speed? Is the road surface flat, smooth or bumpy? When calculating the applied load and the current of the test battery, the simulation will take all factors into account in this performance equation. The experts who conducted the battery test also took this complex interaction into account. For example, the initial required power will vary with the battery temperature or other parameters. Researchers keep track of the actual parameters of the battery, and continue to feed back the parameters to the simulation system. This tracking feedback loop constitutes a hardware-in-the-loop test. Throughout the testing process, the input is not always static data. Instead, it will dynamically adjust based on battery simulation and battery data. The researcher said: “We can reproduce real driving actions in test scenarios, such as uphill or downhill or sharp turns.” We can also study how other variables affect performance, for example, to determine the quality of the vehicle when increased load What happens when you increase it by 20%. Vibration test can also be carried out, using a vibrating meter driven by six hydraulic cylinders, and it can be moved in any direction to simulate the impact of the car chassis on battery movement.
One of the biggest challenges of hardware-in-the-loop testing is that the simulation must be performed in real time. For example, if you conduct a test to investigate a 10-second operation, the entire simulation may not take more than 10 seconds. After all, this is a cyclic test, and the results of the simulation must be directly fed back into the test so that the simulation can be dynamically updated as the test progresses. Researchers have fine-tuned the computational complexity to make it work. The researchers said: “We run simulations according to different levels of complexity to achieve the best balance between complexity and calculation time.” The system is ready to be put into use, and preparations for the final demonstration are still in progress.